Hệ thống xử lý nước cấp Thủy sản Vạn Đức – 90m3/giờ (nước giếng) + 15m3/giờ (nước sông)
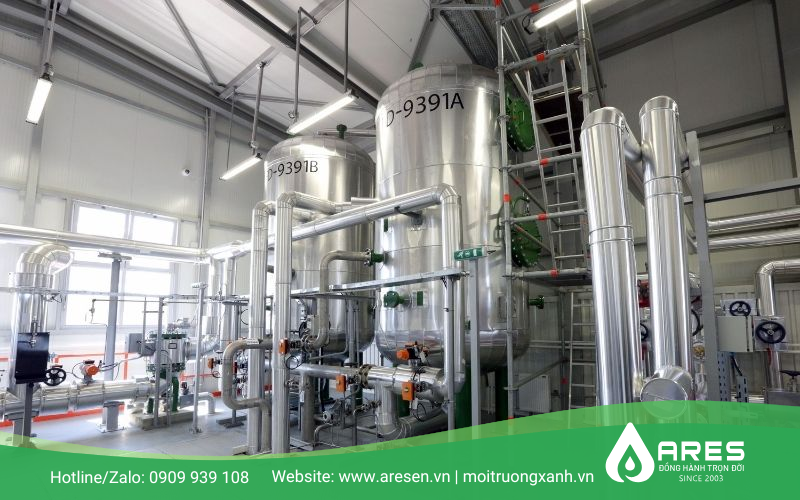
Hệ thống xử lý nước cấp Thủy sản Vạn Đức – 90m3/giờ (nước giếng) + 15m3/giờ (nước sông)
Liên hệ tư vấnCông ty Thủy sản Vạn Đức đối mặt với nhiều thách thức phức tạp trong việc xử lý nước cấp cho nhà máy chế biến thủy sản. Nguồn nước đầu vào bao gồm nước giếng chứa hàm lượng sắt, mangan cao (Fe: 2-5 mg/L, Mn: 0.5-1.2 mg/L) và độ cứng lớn (250-400 mg/L CaCO3), cùng với nước sông có độ đục cao và biến động (50-500 NTU), nhiều chất rắn lơ lửng và nguy cơ nhiễm vi sinh vật. Công ty phải tuân thủ tiêu chuẩn nghiêm ngặt 98/83 EC của Liên minh Châu Âu về nước sử dụng trong chế biến thực phẩm, với các thông số cụ thể như pH 6.5-8.5, độ đục <1 NTU, Fe <0.3 mg/L, Mn <0.1 mg/L, và chỉ số Coliform 0 CFU/100mL. Đồng thời phải đảm bảo công suất xử lý lớn và ổn định (90m3/giờ nước giếng và 15m3/giờ nước sông) để đáp ứng nhu cầu sản xuất liên tục 24/7, trong khi không gian lắp đặt hạn chế và áp lực về chi phí vận hành, bảo trì luôn hiện hữu.
Để giải quyết những thách thức này, Vạn Đức đã triển khai hệ thống xử lý nước cấp toàn diện với hai quy trình riêng biệt. Đối với nước giếng (90m3/giờ), hệ thống gồm hai dây chuyền song song, mỗi dây 45m3/giờ với các bước: hạ nhiệt nước ngầm xuống dưới 32°C qua tháp giải nhiệt; lọc khử sắt qua lớp vật liệu sỏi và cát đặc biệt; làm mềm nước bằng hạt resin trao đổi ion; lọc tinh bằng lõi lọc 5-10 micron làm từ sợi Polypropylene; và khử trùng bằng Chlorine (0.1-1%) với dư lượng kiểm soát ở 0.5-1ppm. Đối với nước sông (15m3/giờ), quy trình gồm keo tụ lắng trong bằng PAC (Poly Aluminium Chloride) - phèn nhôm thế hệ mới có hiệu quả cao hơn phèn sunfat 4-5 lần; lọc thô qua vật liệu sỏi và cát; và lọc tinh qua lõi lọc 5-10 micron. Toàn hệ thống được tích hợp hệ thống kiểm soát tự động với các thiết bị đo lưu lượng, áp suất, và chất lượng nước, cùng tính năng tự động xả rửa ngược và cảnh báo bất thường. Thiết kế tối ưu không gian với bố trí compact và sử dụng bơm hiệu suất cao giúp tiết kiệm năng lượng đáng kể.
Hệ thống đã mang lại những kết quả ấn tượng. Nước cấp cho sản xuất đạt chất lượng vượt tiêu chuẩn với pH 7.0-7.5, độ đục <0.5 NTU, Fe <0.1 mg/L, Mn <0.05 mg/L, độ cứng <50 mg/L CaCO3, và chỉ số Coliform 0 CFU/100mL. Nước cấp cho lò hơi cũng đạt các thông số tối ưu với pH 7.2-7.8, độ đục <2 NTU, Fe <0.2 mg/L, và độ cứng <5 mg/L CaCO3. Hệ thống vận hành ổn định 24/7, đáp ứng 100% nhu cầu nước của công ty với tỷ lệ dừng bảo trì thấp (dưới 5%), và thích ứng tốt với các biến động chất lượng nước đầu vào. Về mặt kinh tế, hệ thống giúp giảm 25-30% lượng hóa chất sử dụng, tiết kiệm 20-25% điện năng, kéo dài tuổi thọ vật liệu lọc và thiết bị sản xuất. Dự án còn đóng góp tích cực vào việc bảo vệ tài nguyên nước, giảm thiểu ô nhiễm, nâng cao chất lượng sản phẩm và môi trường làm việc, trở thành mô hình tiên phong đáng học hỏi cho ngành chế biến thủy sản, đặc biệt với khả năng đáp ứng và vượt tiêu chuẩn 98/83 EC của Liên minh Châu Âu.
Ngành chế biến thủy sản là một trong những ngành công nghiệp mũi nhọn của Việt Nam, đóng góp quan trọng vào kim ngạch xuất khẩu và tạo nhiều việc làm cho người lao động. Tuy nhiên, quá trình chế biến thủy sản đòi hỏi lượng nước sạch lớn và chất lượng cao để đảm bảo an toàn vệ sinh thực phẩm và đáp ứng các tiêu chuẩn quốc tế nghiêm ngặt.
Công ty TNHH Thực phẩm Vạn Đức, một trong những doanh nghiệp hàng đầu trong lĩnh vực chế biến và xuất khẩu thủy sản đông lạnh tại Việt Nam, đã nhận thức rõ tầm quan trọng của nguồn nước sạch trong quy trình sản xuất. Để đảm bảo chất lượng sản phẩm và tuân thủ các tiêu chuẩn nghiêm ngặt của thị trường quốc tế, công ty đã đầu tư xây dựng hệ thống xử lý nước cấp hiện đại với công suất 90m3/giờ (xử lý nước giếng) và 15m3/giờ (xử lý nước sông).
Bài viết này sẽ phân tích chi tiết về hệ thống xử lý nước cấp tại Công ty Thủy sản Vạn Đức, từ những thách thức đặc thù, giải pháp công nghệ được áp dụng, đến kết quả đạt được sau khi triển khai hệ thống. Đây không chỉ là một dự án kỹ thuật đơn thuần mà còn là minh chứng cho cam kết của doanh nghiệp về chất lượng sản phẩm và phát triển bền vững.
Thách thức
1. Đặc điểm nguồn nước đầu vào phức tạp
Công ty Thủy sản Vạn Đức sử dụng hai nguồn nước chính cho quy trình sản xuất: nước giếng và nước sông, mỗi nguồn đều có những đặc điểm và thách thức riêng:
Nước giếng: Mặc dù nước giếng thường có độ trong cao hơn so với nước mặt, nhưng nguồn nước ngầm tại khu vực của nhà máy chứa hàm lượng sắt, mangan cao và độ cứng lớn. Cụ thể, nước giếng có thể chứa:
- Hàm lượng sắt (Fe): 2-5 mg/L, vượt nhiều lần so với tiêu chuẩn nước cấp cho chế biến thủy sản (<0.3 mg/L)
- Hàm lượng mangan (Mn): 0.5-1.2 mg/L, cao hơn giới hạn cho phép (<0.1 mg/L)
- Độ cứng tổng: 250-400 mg/L CaCO3, cần được làm mềm để đảm bảo hiệu quả sử dụng
Nước sông: Nguồn nước sông được sử dụng như một nguồn bổ sung, nhưng có những thách thức lớn hơn:
- Độ đục cao và biến động theo mùa (50-500 NTU)
- Nhiều chất rắn lơ lửng, cặn bã hữu cơ
- Khả năng nhiễm vi sinh vật cao
- Chất lượng không ổn định, phụ thuộc vào điều kiện thời tiết và các hoạt động xả thải ở thượng nguồn
2. Yêu cầu nghiêm ngặt về chất lượng nước đầu ra
Là doanh nghiệp chế biến thủy sản xuất khẩu, Vạn Đức phải tuân thủ những tiêu chuẩn rất nghiêm ngặt về chất lượng nước sử dụng trong quá trình sản xuất:
Tiêu chuẩn quốc tế: Đáp ứng tiêu chuẩn 98/83 EC của Liên minh Châu Âu về nước sử dụng trong chế biến thực phẩm, với các thông số cụ thể:
- pH: 6.5-8.5
- Độ đục: < 1 NTU
- Độ màu: < 5 Pt-Co
- Hàm lượng sắt: < 0.3 mg/L
- Hàm lượng mangan: < 0.1 mg/L
- Độ cứng: < 100 mg/L CaCO3
- Chỉ số Coliform: 0 CFU/100mL
Yêu cầu phân loại chất lượng nước: Cần phân loại và cung cấp nước với các chất lượng khác nhau cho các công đoạn sản xuất khác nhau:
- Nước dùng cho sản xuất chế biến: tiêu chuẩn cao nhất, đáp ứng các yêu cầu về vi sinh và hóa lý
- Nước cấp cho lò hơi: cần loại bỏ hoàn toàn độ cứng, có thể chấp nhận một số thông số khác ở mức độ phù hợp
3. Công suất xử lý lớn và ổn định
Với quy mô sản xuất lớn của Công ty Vạn Đức, hệ thống xử lý nước cấp phải đáp ứng những yêu cầu khắt khe về công suất:
Nhu cầu nước liên tục: Quá trình sản xuất chế biến thủy sản diễn ra liên tục 24/7, đòi hỏi nguồn nước cấp ổn định không gián đoạn. Bất kỳ sự cố nào dẫn đến thiếu nước đều có thể gây thiệt hại lớn về kinh tế và ảnh hưởng đến chất lượng sản phẩm.
Dao động theo mùa vụ sản xuất: Nhu cầu nước có thể tăng đột biến trong các thời điểm cao điểm sản xuất, đòi hỏi hệ thống phải có khả năng đáp ứng linh hoạt với các dao động này.
Nhu cầu tổng hợp: Công ty cần đồng thời 90m3/giờ nước giếng đã qua xử lý cho dây chuyền sản xuất chính và 15m3/giờ nước sông đã qua xử lý để cung cấp cho lò hơi và các hoạt động phụ trợ khác.
4. Không gian lắp đặt hạn chế
Nhà máy Vạn Đức đối mặt với thách thức về mặt bằng cho hệ thống xử lý nước cấp:
Diện tích hạn chế: Không gian nhà máy có giới hạn, trong khi vẫn cần ưu tiên cho các hoạt động sản xuất chính.
Yêu cầu tối ưu hóa: Cần thiết kế hệ thống gọn gàng, hiệu quả, tối ưu hóa không gian sử dụng mà vẫn đảm bảo công suất và chất lượng xử lý.
5. Chi phí vận hành và bảo trì
Một thách thức quan trọng khác là đảm bảo chi phí vận hành và bảo trì hợp lý:
Chi phí hóa chất: Xử lý nước cấp đòi hỏi sử dụng nhiều loại hóa chất khác nhau, có thể tạo gánh nặng chi phí nếu không được tối ưu hóa.
Tiêu thụ năng lượng: Hệ thống bơm, thiết bị lọc và các thiết bị khác tiêu thụ lượng điện năng đáng kể, cần được thiết kế để tiết kiệm năng lượng.
Nhu cầu bảo trì thường xuyên: Các thiết bị lọc, đặc biệt là lõi lọc và vật liệu lọc, cần được vệ sinh và thay thế định kỳ, đòi hỏi chi phí và nhân lực.
Giải pháp
Để giải quyết những thách thức nêu trên, Công ty Thủy sản Vạn Đức đã hợp tác với các chuyên gia môi trường để thiết kế và triển khai một hệ thống xử lý nước cấp toàn diện, kết hợp nhiều công nghệ tiên tiến.
1. Hệ thống xử lý nước giếng (90m3/giờ)
1.1. Quy trình xử lý chính
Hệ thống xử lý nước giếng được thiết kế với công suất 90m3/giờ, bao gồm hai dây chuyền lọc vận hành song song, mỗi dây chuyền 45m3/giờ, theo trình tự: lọc khử sắt → làm mềm → lọc tinh → khử trùng.
Bước 1: Hạ nhiệt nước ngầm
- Nước giếng sau khi bơm lên được đưa qua tháp giải nhiệt để hạ nhiệt xuống dưới 32°C
- Giúp tăng hiệu quả xử lý ở các công đoạn sau và đảm bảo điều kiện nhiệt độ phù hợp cho quá trình sản xuất
Bước 2: Lọc khử sắt
- Nước đi qua hệ thống bồn lọc với các lớp vật liệu lọc đặc biệt gồm sỏi lọc nước và cát lọc
- Công dụng: khử hoàn toàn sắt, giảm hàm lượng nhiễm bẩn của các hợp chất hữu cơ, khử các kim loại nặng như đồng, kẽm, crom, niken
- Đồng thời hấp thụ khoảng 90% hàm lượng dầu, đảm bảo an toàn cho sử dụng cấp nước sản xuất chế biến thủy sản đông lạnh
- Kéo dài tuổi thọ của lõi lọc 5-10 micron ở công đoạn sau
Bước 3: Làm mềm nước
- Nước sau lọc khử sắt đi qua thiết bị làm mềm chứa các hạt resin
- Cơ chế: thông qua quá trình trao đổi ion, hạt resin giữ lại trên bề mặt các ion tạo nên độ cứng của nước (Ca2+, Mg2+), đồng thời phóng thích ion Na+
- Hạt resin được phục hồi định kỳ bằng dung dịch muối NaCl
- Hiệu quả: giảm đáng kể độ cứng của nước, bảo vệ thiết bị và đường ống khỏi cặn canxi, magiê
Bước 4: Lọc tinh
- Nước sau làm mềm đi vào thiết bị lọc tinh được trang bị các lõi lọc 5-10 micron làm bằng sợi Polypropylene
- Thiết bị này giữ lại toàn bộ các hạt cặn và lơ lửng còn lại trong nước có kích thước lớn hơn 5-10 micron
- Lõi lọc được thay thế hoặc tái sinh định kỳ bằng dung dịch acid HCl loãng
- Nước sau lọc tinh đạt cơ bản các chỉ tiêu hóa lý, đủ điều kiện cấp cho quá trình sản xuất
Bước 5: Khử trùng
- Sử dụng Chlorine để khử trùng nước sau khi qua các quy trình lọc
- Nồng độ dung dịch pha loãng 0,1-1%
- Kiểm soát dư lượng clo của nước sau xử lý nằm trong khoảng cho phép (0,5-1ppm)
- Đảm bảo nước đạt tiêu chuẩn 98/83 EC cả về chỉ tiêu hóa lý và vi sinh
2. Hệ thống xử lý nước sông (15m3/giờ)
Với nước sông có đặc tính khác biệt, quy trình xử lý được thiết kế riêng để đảm bảo hiệu quả, tập trung vào xử lý độ đục cao và các tạp chất đặc trưng của nước mặt, chủ yếu để cấp cho lò hơi.
2.1. Quy trình keo tụ lắng trong
Bước 1: Keo tụ
- Keo tụ là quá trình trước tiên, rất cần thiết trong công nghệ xử lý nước cấp từ nước sông
- Nguyên lý: cho vào nước một loại hóa chất có tác dụng làm cho nhiều hạt huyền phù nhỏ kết hợp lại thành những hạt lớn hơn và nặng hơn
- Hóa chất được lựa chọn: Poly Aluminium Chloride (PAC) – phèn nhôm thế hệ mới dạng cao phân tử, có nhiều ưu điểm hơn so với phèn nhôm sunphat truyền thống:
- Hiệu quả lắng trong cao hơn 4-5 lần
- Thời gian keo tụ nhanh hơn
- Ít làm biến động pH của nước
- Không cần hoặc dùng ít chất hỗ trợ
- Không bị cục khi dùng thiếu hoặc thừa PAC
- Khả năng loại bỏ các chất hữu cơ hòa tan và không hòa tan cùng kim loại nặng tốt hơn phèn sunfat
Bước 2: Lắng trong
- Nước sau keo tụ được đưa vào bể lắng, cho phép các bông cặn có kích thước và khối lượng lớn lắng xuống đáy
- Lớp nước trong phía trên được thu và dẫn sang công đoạn tiếp theo
- Bùn cặn được định kỳ xả thải và xử lý theo quy định
2.2. Quy trình lọc đa cấp
Bước 1: Lọc thô
- Nước sau lắng đi qua các lớp vật liệu lọc bao gồm sỏi lọc nước và cát lọc
- Tương tự như công đoạn lọc khử sắt của nước giếng, giúp loại bỏ sắt, các hợp chất hữu cơ, kim loại nặng và giảm đáng kể hàm lượng dầu
- Đặc biệt hiệu quả trong việc giảm tải và bảo vệ màng lọc của các lõi lọc 5-10 micron ở công đoạn sau
Bước 2: Lọc tinh
- Nước sau lọc thô đi vào thiết bị lọc tinh với lõi lọc 5-10 micron làm bằng sợi Polypropylene
- Giữ lại toàn bộ các hạt cặn và lơ lửng có kích thước lớn hơn 5-10 micron
- Lõi lọc được vệ sinh định kỳ bằng dung dịch acid HCl loãng
- Nước sau lọc tinh đạt tiêu chuẩn cho nước cấp lò hơi
3. Hệ thống kiểm soát và tự động hóa
Để đảm bảo vận hành ổn định và hiệu quả, hệ thống được trang bị các thiết bị kiểm soát và tự động hóa:
Kiểm soát lưu lượng: Lắp đặt các đồng hồ đo lưu lượng tại các điểm quan trọng trong hệ thống để giám sát và điều chỉnh lưu lượng nước.
Kiểm soát áp suất: Hệ thống cảm biến áp suất giúp phát hiện sớm các vấn đề như tắc nghẽn lõi lọc hoặc vật liệu lọc.
Kiểm soát chất lượng nước: Lắp đặt thiết bị đo các thông số quan trọng như pH, độ đục, clo dư để đảm bảo nước đạt tiêu chuẩn trước khi cung cấp cho sản xuất.
Tự động hóa xả rửa ngược: Các bồn lọc được thiết kế với khả năng tự động rửa ngược theo thời gian hoặc theo sự sụt giảm áp suất, giúp kéo dài tuổi thọ của vật liệu lọc.
Hệ thống cảnh báo: Khi phát hiện bất thường về lưu lượng, áp suất hoặc chất lượng nước, hệ thống sẽ phát tín hiệu cảnh báo cho người vận hành.
4. Thiết kế tối ưu không gian và năng lượng
Hệ thống được thiết kế với sự chú trọng đến việc tối ưu hóa không gian và tiết kiệm năng lượng:
- Thiết kế compact: Các thiết bị được bố trí hợp lý, tận dụng không gian theo chiều cao khi có thể.
- Sử dụng bơm hiệu suất cao: Lựa chọn các loại bơm có hiệu suất cao, tiết kiệm điện năng.
- Tái sử dụng nước rửa ngược: Nước từ quá trình rửa ngược các bồn lọc được thu gom, xử lý sơ bộ và tái sử dụng khi có thể, giúp tiết kiệm nước.
- Tối ưu hóa quá trình phục hồi resin: Áp dụng công nghệ phục hồi resin tiên tiến, giúp tiết kiệm muối và nước sử dụng.
Kết quả
1. Chất lượng nước đạt chuẩn cao
Sau khi hệ thống xử lý nước cấp được đưa vào vận hành tại Công ty Thủy sản Vạn Đức, chất lượng nước đã đạt được những kết quả ấn tượng:
Nước cấp cho sản xuất (từ nguồn nước giếng):
- pH: 7.0-7.5 (tiêu chuẩn: 6.5-8.5)
- Độ đục: < 0.5 NTU (tiêu chuẩn: < 1 NTU)
- Hàm lượng sắt: < 0.1 mg/L (tiêu chuẩn: < 0.3 mg/L)
- Hàm lượng mangan: < 0.05 mg/L (tiêu chuẩn: < 0.1 mg/L)
- Độ cứng: < 50 mg/L CaCO3 (tiêu chuẩn: < 100 mg/L CaCO3)
- Chỉ số Coliform: 0 CFU/100mL (tiêu chuẩn: 0 CFU/100mL)
Nước cấp cho lò hơi (từ nguồn nước sông):
- pH: 7.2-7.8
- Độ đục: < 2 NTU
- Hàm lượng sắt: < 0.2 mg/L
- Độ cứng: < 5 mg/L CaCO3
- Chỉ số Coliform: 0 CFU/100mL
Với chất lượng nước đạt và vượt tiêu chuẩn 98/83 EC của Liên minh Châu Âu, hệ thống đã đáp ứng đầy đủ yêu cầu nghiêm ngặt về nước sử dụng trong chế biến thực phẩm, góp phần đảm bảo chất lượng và an toàn vệ sinh thực phẩm cho sản phẩm của Vạn Đức.
2. Vận hành ổn định với công suất cao
Hệ thống xử lý nước cấp tại Vạn Đức đã chứng minh được tính ổn định và hiệu quả trong vận hành:
Công suất đáp ứng đầy đủ:
- Xử lý ổn định 90m3/giờ nước giếng cho sản xuất chính
- Xử lý ổn định 15m3/giờ nước sông cho lò hơi và hoạt động phụ trợ
- Khả năng đáp ứng 100% nhu cầu nước của công ty trong mọi điều kiện sản xuất
Độ tin cậy cao: Hệ thống vận hành liên tục 24/7 với tỷ lệ thời gian dừng để bảo trì thấp (dưới 5% thời gian vận hành).
Khả năng thích ứng tốt: Ngay cả khi có sự dao động về chất lượng nước đầu vào (đặc biệt là nước sông trong mùa mưa), hệ thống vẫn duy trì chất lượng nước đầu ra ổn định.
3. Hiệu quả kinh tế và tiết kiệm chi phí
Bên cạnh việc đảm bảo chất lượng nước, hệ thống còn mang lại những lợi ích kinh tế đáng kể:
Giảm chi phí xử lý nước:
- Giảm 25-30% lượng hóa chất sử dụng nhờ thiết kế tối ưu và kiểm soát định lượng chính xác
- Tiết kiệm 20-25% điện năng so với các hệ thống truyền thống nhờ sử dụng thiết bị hiệu suất cao
- Kéo dài tuổi thọ vật liệu lọc và resin nhờ quy trình vận hành và bảo trì khoa học
Giảm tác động đến sản xuất:
- Giảm thiểu thời gian dừng sản xuất do thiếu nước hoặc nước không đạt chuẩn
- Tăng tuổi thọ thiết bị sản xuất nhờ nguồn nước chất lượng cao, ít cặn và ăn mòn
Tối ưu hóa không gian: Thiết kế gọn gàng, hiệu quả giúp tiết kiệm diện tích sàn quý giá cho các hoạt động sản xuất chính.
4. Tác động tích cực đến môi trường và xã hội
Hệ thống xử lý nước cấp tại Vạn Đức không chỉ mang lại lợi ích kinh tế trực tiếp mà còn có những đóng góp tích cực cho môi trường và xã hội:
Bảo vệ tài nguyên nước: Giảm áp lực lên nguồn nước ngầm nhờ kết hợp sử dụng cả nước giếng và nước sông, đồng thời tối ưu hóa việc sử dụng nước trong quá trình sản xuất.
Giảm thiểu ô nhiễm: Giảm lượng nước thải và tải lượng ô nhiễm cần xử lý nhờ việc sử dụng nước hiệu quả hơn.
Nâng cao chất lượng sản phẩm: Nước sạch đạt chuẩn cao góp phần đảm bảo an toàn vệ sinh thực phẩm, bảo vệ sức khỏe người tiêu dùng.
Tạo môi trường làm việc tốt hơn: Cung cấp nước sạch cho các hoạt động vệ sinh nhà xưởng, thiết bị và cá nhân, góp phần tạo môi trường làm việc sạch sẽ, an toàn cho người lao động.
5. Mô hình cho ngành chế biến thủy sản
Thành công của hệ thống xử lý nước cấp tại Công ty Thủy sản Vạn Đức đã trở thành một mô hình đáng tham khảo cho nhiều doanh nghiệp trong ngành:
Mô hình tiên phong: Đây là một trong những hệ thống xử lý nước cấp công suất lớn, kết hợp xử lý cả nước giếng và nước sông, được áp dụng trong ngành chế biến thủy sản tại Việt Nam.
Tiêu chuẩn cao: Đáp ứng và vượt các tiêu chuẩn quốc tế nghiêm ngặt, phù hợp với xu hướng hội nhập và xuất khẩu của ngành thủy sản Việt Nam.
Tính linh hoạt cao: Thiết kế dạng mô-đun cho phép dễ dàng nhân rộng hoặc điều chỉnh theo nhu cầu cụ thể của từng doanh nghiệp.
Kết luận
Hệ thống xử lý nước cấp tại Công ty Thủy sản Vạn Đức với công suất 90m3/giờ (nước giếng) và 15m3/giờ (nước sông) là một minh chứng thành công về việc áp dụng công nghệ tiên tiến để giải quyết những thách thức đặc thù trong ngành chế biến thủy sản. Dự án đã giải quyết hiệu quả các vấn đề về đặc điểm nguồn nước đầu vào phức tạp, yêu cầu nghiêm ngặt về chất lượng nước đầu ra, và nhu cầu công suất lớn, ổn định.
Thành công của dự án không chỉ nằm ở việc đáp ứng các tiêu chuẩn kỹ thuật mà còn ở hiệu quả kinh tế và tác động tích cực đến môi trường. Với chất lượng nước đạt và vượt tiêu chuẩn 98/83 EC của Liên minh Châu Âu, hệ thống đã góp phần quan trọng vào việc đảm bảo chất lượng sản phẩm thủy sản của Vạn Đức, nâng cao khả năng cạnh tranh trên thị trường quốc tế.
Việc kết hợp sử dụng hai nguồn nước (giếng và sông) với công nghệ xử lý phù hợp cho từng loại là một giải pháp thông minh, giúp tối ưu hóa việc sử dụng tài nguyên nước, giảm áp lực lên nguồn nước ngầm, đồng thời đảm bảo nguồn cung cấp nước ổn định cho hoạt động sản xuất.
Hệ thống xử lý nước cấp tại Vạn Đức không chỉ là một giải pháp kỹ thuật đơn thuần mà còn là minh chứng cho cam kết của doanh nghiệp về chất lượng sản phẩm và phát triển bền vững. Đây là mô hình đáng để các doanh nghiệp trong ngành chế biến thủy sản và các ngành công nghiệp thực phẩm khác tham khảo và học hỏi.
Với tầm nhìn dài hạn, Công ty Thủy sản Vạn Đức đã chứng minh rằng đầu tư cho hệ thống xử lý nước cấp hiện đại không chỉ là một chi phí mà còn là một chiến lược kinh doanh thông minh, mang lại lợi ích lâu dài về chất lượng sản phẩm, hiệu quả sản xuất và bảo vệ môi trường.